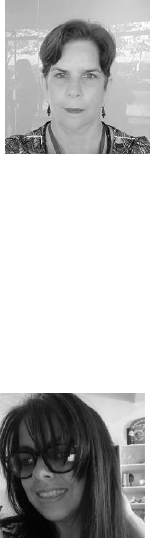
189
Scientia et Technica Año XXVIII, Vol. 28, No. 04, octubre-diciembre de 2023. Universidad Tecnológica de Pereira.
[11] Gestión de la I+D+i: Terminología y definiciones de las actividades de
I+D+i, NC 1306:2019, Oficina Nacional de Normalización, La Habana,
2019.
[12] Gestión de la I+D+i: Requisitos del sistema de I+D+i, NC 1307:2019,
Oficina Nacional de Normalización, La Habana, 2019.
[13] Gestión de la I+D+i: Sistema de vigilancia e inteligencia, NC 1308:2019,
Oficina Nacional de Normalización, La Habana, 2019.
[14] C. F. Poltronieri, M. C. Gerolamo, and L. C. Carpinetti, “An instrument
for the assessment of management systems integration,” Gestão Produção
São Carlos, vol. 24, no. 4, pp. 638-652. DOI: 10.1590/0104-530X1697-
14
[15] S. Talapatra; G. Santos; K. Uddin, and F. Carvalho, “International Main
benefits of integrated management systems through literature review,”
Journal for Quality Research, vol. 13, no. 4, pp. 1037–1054, December,
2019. DOI: 10.24874/IJQR13.04-19
[16] R. M. Guerra Bretaña, and M. C. Meizoso Valdés, “Gestión de la calidad.
Conceptos, principios, modelos y herramientas,” 2nd ed., La Habana:
Editorial UH, 2019.
[17] M. C. Meizoso Valdés, and R. M. Guerra Bretaña, “Implantación de
Sistemas Integrados de gestión. Un reto a la empresa cubana,”
Normalización, no. 1, pp. 33-42, 2019.
[18] J. R. Ramírez García, and R. M. Guerra Bretaña, “La Gestión de la I+D+I:
Una decisión estratégica,” EKOtemas, vol. 3, no. 3, pp. 25-30,
septiembre-diciembre, 2017.
[19] R. M. Guerra Bretaña, and J. R. Ramírez García, “Empresa: ¿innovación
y calidad o innovación vs calidad?,” In R. Torres Pérez, and D. Echevarría
León, Miradas a la economía cubana. Un acercamiento a la
«actualización» seis años después, La Habana, Cuba: Ruth Editorial,
2017, pp. 95-104.
[20] A. Hernandez-Vivanco A., M. Bernardo, and C. Cruz-Cásarez,
(2016),"Relating open innovation, innovation and management systems
integration", Industrial Management & Data Systems, vol. 116, no. 8, pp.
1540-1556, DOI: 10.1108/IMDS-09-2015-0405
[21] B. Manders, H. J. de Vries, and K Blind, “ISO 9001 and product
innovation: A literature review and research framework,” Technovation,
vol 48–49, pp 41–55, February–March 2016. DOI:
10.1016/j.technovation.2015.11.004
[22] R. M. Guerra Bretaña, D. M. Montoya Quintero, and J. R. Ramírez
García, “El enfoque de la gestión de la calidad basado en la gestión del
conocimiento y de la innovación,” In Ciencias económicas y contables
desafíos y retos para la competitividad, Medellín, Colombia: Sello
Editorial Coruniamericana, 2020, pp. 66-85.
[23] L. K. H. Lai, “Integration of Quality and Innovation Management System
for Organization Innovation,” Proceedings of the 13th ANQ Congress,
Taipei, Taiwan, September 23-24, 2015.
[24] D. Maier, I. Sven-Joachim, A. Fortmüller, and A. Maier, “Development
and Operationalization of a Model of Innovation Management System as
Part of an Integrated Quality-Environment-Safety System,” The
Amfiteatru Economic Journal, vol. 19, no. 44, pp. 302-314, February,
2017. [Online]. Available:
https://www.amfiteatrueconomic.ro/temp/Journal_no_44.pdf
[25] L. F. Á Becerra, O. A. M. Andrade, and G. L. I. Díaz, “Sistema de gestión
de la calidad para el proceso de investigación: Universidad de Otavalo,
Ecuador,” Revista Actualidades investigativas en educación, vol. 19, no.
1, pp. 1-32. DOI: 10.15517/aie.v19i1.35235
[26] R. M. Guerra Bretaña, and M. C. Meizoso Valdés, “Calidad, innovación
y mejora continua. Análisis de caso de innovación organizacional,”
Revista Cubana de Educación Superior, 2010-2011, pp.174-190, 2013.
[27] R. M. Guerra Bretaña, M. B. Valencia Bonilla, N. Martínez Alfonso, “La
innovación y la gestión de la calidad universitaria, sus vínculos con la
mejora del desempeño y el impacto social,” 11no Congreso Internacional
de Educación Superior U´2018, La Habana, Cuba, 2018.
[28] R. M. Guerra Bretaña. J. R. Ramírez García, F. J. Ramos Azcuy.
Relaciones entre la gestión de la calidad, el conocimiento y la
innovación,” 12vo Congreso Internacional de Educación Superior
U´2020, La Habana, Cuba, 2020.
[29] R. M. Guerra Bretaña, “Ciencia, innovación tecnológica y sociedad:
experiencias del Centro de Biomateriales,” Universidad de La Habana,
no. 271, pp. 34-55, 2010.
[30] R. M. Guerra Bretaña, and Y. Veranes Pantoja, “La gestión de la
innovación en el Centro de Biomateriales de la Universidad de La
Habana,” II Convención Internacional de Calidad “Habana 2019”, La
Habana, Cuba, 2019.
[31] Sistemas de gestión de la calidad. Requisitos, NC-ISO 9001:2015,
Oficina Nacional de Normalización, La Habana, Cuba, 2015.
[32] R. M. Guerra Bretaña, “Normalización, calidad y gestión de riesgos en el
campo de los dispositivos médicos: metodologías y estudio de casos”, La
Habana, Cuba, Editorial UH, 2019.
[33] Equipos Médicos. Sistemas de gestión de la calidad. Requisitos para
propósitos reglamentarios, NC-ISO 13485:2018, Oficina Nacional de
Normalización, La Habana, Cuba, 2018.
[34] Biomat, Manual de Gestión, Ed. 9, Mod. 01, La Habana, Cuba, marzo,
2021.
[35] Biomat, Procedimiento del Sistema PS 08 Estrategia del diseño y
desarrollo, Ed. 5, La Habana, Cuba, julio, 2019.
[36] R. M. Guerra Bretaña, and A. L. Flórez Rendón, “Impact of regulations
on innovation in the field of medical devices,” Research on Biomedical
Engineering, vol. 34, no. 4, pp. 356-367, October-December, 2018. DOI:
10.1590/2446-4740.180054
[37] Innovation Counsellors LLC, A Future at Risk: Economic Performance,
Entrepreneurship, and Venture Capital in the U.S. Medical Technology
Sector, Minneapolis, Minnesota, 2016. [Online]. Available:
https://www.medtechcorekpi.org.nz/edit/library/docs/Advamed2016Afut
ureatrisk.pdf
[38] A. Mardani, S. Nikoosokhan, M. Moradi, and M. Doustar, “The
Relationship Between Knowledge Management and Innovation
Performance,” Journal of High Technology Management Research, vol.
29, pp. 12–26. DOI: 10.1016/j..hitech.2018.04.002.
[39] A. M. Acosta Soto, R. M. Guerra Bretaña, J. R. Ramírez García, “La
gestión integral de los riesgos en el Centro de Biomateriales de la
Universidad de La Habana,” Revista Caribeña de Ciencias Sociales, June,
2018. [Online]. Available:
https://www.eumed.net/rev/caribe/2018/06/gestion-integral-riesgos.html
[40] Knowledge management systems — Requirements, ISO 30401:2018,
International Organization for Standardization, Genève, 2018.
Rosa Mayelin Guerra Bretaña was born
in Havana, Cuba in 1957. She received
degree in Physics from the State
University of San Petersburg, Russia in
1982, and the doctorate degree in
Chemistry in 1991 at de National Centre
from Scientific Research in Cuba. Since
1991 she works at de Centre of
Biomaterials of the Havana University. In 1997 Dr. Guerra
received the scientific category of Titular Researcher. In 2018
she received the teaching category Titular Professor. Currently,
her research interests include quality management, innovation
management, metrology, normalization and integrated
management systems.
ORCID: https://orcid.org/0000-0002-0561-6678
Maelys Hernández Almaguer was born
in Havana, Cuba, on August 4, 1986. She
graduated in pharmaceutical sciences in
2009 from the Faculty of Pharmacy and
Food of the University of Havana. From
2009 to 2019 she was a researcher at the
Quality Management Department of the
AIDS Research Laboratory (LISIDA). In 2016 she obtained a
degree of Magister in Quality and Environmental Management
at the University of Havana. Since 2020, she is a professor at
the Institute of Pharmacy and Food at the University of Havana.
ORCID: https://orcid.org/0000-0002-2727-2183